What Is a Safe Cable Bending Radius — and Why Should You Care?
Curious about how much you can bend a cable without damaging it? Discover what a safe cable bending radius is, why it matters for performance and safety, and how to follow IEC and NEC standards. Learn practical tips for installers and cable users to avoid costly failures.
hongjing.Wang@Feichun
7/16/202511 min read
Introduction: Why Cable Bending Radius Matters
Picture this: You're installing a critical power cable in a tight electrical panel, and you need to make a sharp turn to reach the connection point. The cable seems flexible enough, so you bend it around a corner that's barely wider than the cable itself. Everything appears fine initially, but six months later, you're dealing with intermittent power failures, overheating, and eventually a complete system shutdown that costs thousands in downtime.
This scenario plays out more often than you might think, and it all comes down to one crucial concept that many installers and engineers overlook: the safe cable bending radius.
When cables are bent incorrectly—beyond their safe mechanical limits—a cascade of problems begins. The outer materials stretch and crack, the inner conductors compress and deform, and the insulation that protects against electrical faults begins to fail. What starts as a seemingly minor installation shortcut can lead to catastrophic failures, safety hazards, and expensive replacements.
The importance of proper cable bending extends across all cable types, but it's particularly critical for power cables that carry high voltages and currents, fiber optic cables that transmit delicate light signals, and flexible cables used in mobile applications where repeated movement is expected. Whether you're an electrical contractor working on commercial buildings, a data center designer routing thousands of network cables, or a port crane installer dealing with heavy-duty power cables, understanding safe bending practices isn't just good practice—it's essential for safety and reliability.
This knowledge is equally valuable for engineers who design cable routing systems, procurement professionals who specify cable requirements, and facility managers who need to understand why proper cable management matters for long-term operational success.
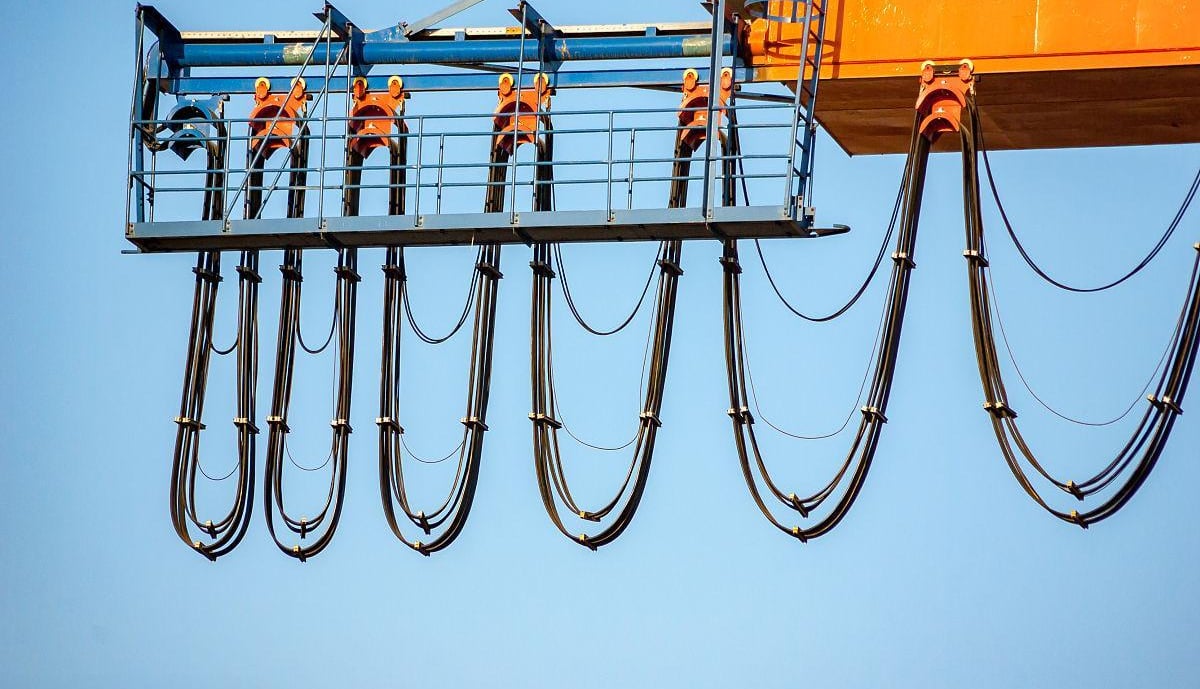
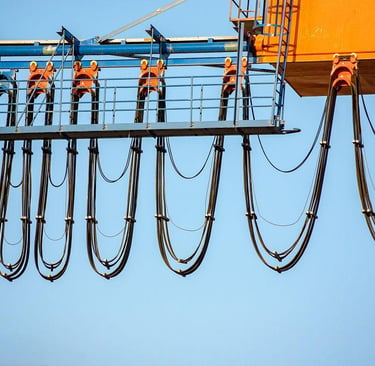
What Is a Cable Bending Radius?
The cable bending radius is fundamentally about respecting the physical limits of materials. When we talk about a "safe" bending radius, we're referring to the minimum radius that a cable can be bent without causing structural damage or performance degradation.
The technical definition follows a simple but crucial formula:
Bending Radius = X × Cable OD
Where:
X = Bending factor (typically ranging from 4 to 15)
OD = Outer diameter of the cable
The bending factor "X" isn't arbitrary—it's determined by the cable's construction, materials, and intended application. A flexible cable used in a robotic arm might have a bending factor of 4, allowing tighter bends because it's designed for movement. Conversely, an armored power cable might require a bending factor of 12 or more because its steel armor and thick insulation need much gentler curves to avoid damage.
It's crucial to understand that this rule applies differently during installation versus operation. During installation, cables typically need to accommodate the minimum bending radius as they're routed through conduits, around corners, and into panels. However, some cables have different requirements for dynamic bending (repeated flexing during operation) versus static installation bending.
The bending radius also relates to the bending diameter, which is simply twice the radius. If a cable has a minimum bending radius of 120mm, its bending diameter would be 240mm. This distinction matters when you're planning cable routes through tight spaces or designing cable management systems.
What Happens If You Bend Too Much?
Understanding the consequences of excessive bending helps explain why these guidelines exist in the first place. When a cable is bent beyond its safe radius, several destructive processes begin simultaneously.
From a mechanical perspective, the materials on the outer side of the bend experience tensile stress—they're being stretched beyond their elastic limits. This stretching can cause micro-cracks in the insulation, particularly in polymer materials that become brittle over time or in cold conditions. These cracks might not be immediately visible, but they create pathways for moisture ingress, which can lead to insulation failure and electrical faults.
Meanwhile, the inner side of the bend experiences compression forces. Conductors can be squeezed into oval shapes, which increases their electrical resistance and can cause hot spots. In extreme cases, individual conductor strands can break, further increasing resistance and heat generation. Composite materials in the cable construction can also be compressed beyond their recovery point, leading to permanent deformation.
The electrical impacts are equally serious. In data and communication cables, excessive bending can cause signal loss, increased bit error rates, and electromagnetic interference (EMI) problems. The precise geometry required for proper signal transmission becomes disrupted, leading to reflection, attenuation, and crosstalk issues.
For power cables, the consequences can be even more severe. Damaged insulation can lead to short circuits, ground faults, or arc faults. The increased resistance from compressed conductors generates heat, which accelerates insulation degradation in a dangerous cycle. In worst-case scenarios, this can lead to cable fires or electrical explosions.
Long-term consequences compound these immediate effects. Cables that have been over-bent experience accelerated aging, higher failure rates, and unpredictable performance. The initial cost savings from taking shortcuts during installation pale in comparison to the expense of premature cable replacement, system downtime, and potential safety incidents.
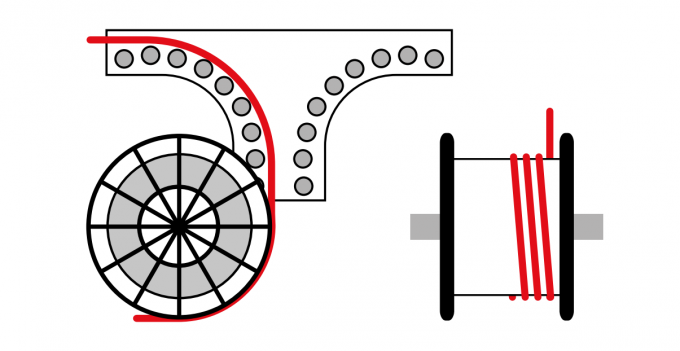
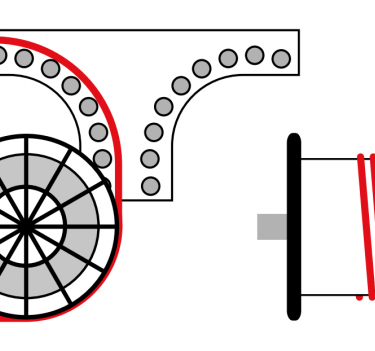
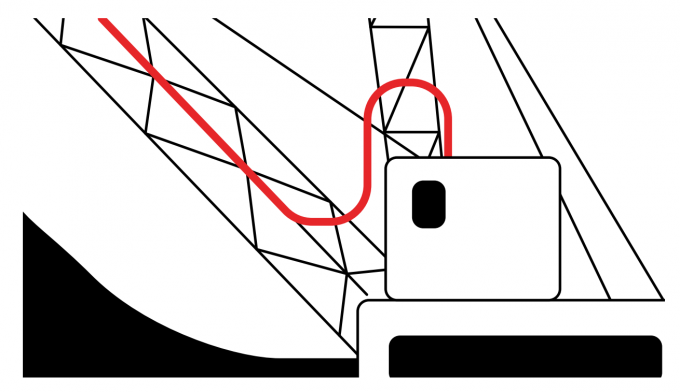
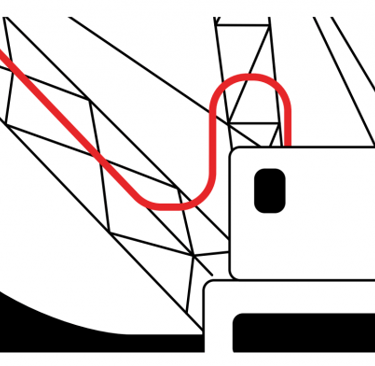
Safe Bending Radius Guidelines by Cable Type
Different cable types have evolved to serve specific purposes, and their bending radius requirements reflect their construction and intended applications. Understanding these differences helps ensure proper installation and long-term reliability.
Unarmoured Power Cables (6× OD)
Standard unarmoured power cables typically require a minimum bending radius of 6 times their outer diameter. These cables are commonly used in building electrical systems, industrial installations, and general power distribution. Their relatively flexible construction allows for moderate bending, but the 6× OD rule ensures that the insulation and conductor geometry remain intact during installation.
Armoured Cables (12× OD)
Armoured cables incorporate steel wire armor or steel tape armor for mechanical protection, making them significantly more rigid than their unarmoured counterparts. The 12× OD requirement reflects this increased rigidity—the armor cannot be bent as sharply without risking damage to both the armor itself and the internal conductors. These cables are commonly used in underground installations, hazardous environments, and applications where mechanical protection is paramount.
Flexible Cables (4–6× OD)
Flexible cables are specifically designed for applications requiring frequent movement or tight routing. Used in robotics, mobile equipment, and temporary installations, these cables employ stranded conductors, special insulation compounds, and flexible sheathing materials. Their 4–6× OD requirement reflects their enhanced flexibility, but even these cables have limits that must be respected.
Fiber Optic Cables (10–20× OD)
Fiber optic cables present unique challenges because they transmit light signals through glass fibers that can be damaged by micro-bending. The 10–20× OD range reflects the critical nature of maintaining proper geometry for optical transmission. Tight bends can cause signal attenuation, increased bit error rates, and complete signal loss. The specific requirement depends on the fiber type, with single-mode fibers typically requiring larger bending radii than multimode fibers.
Data/LAN Cables (4× OD minimum)
Network cables like Cat6 and Cat7 have precise geometric requirements for maintaining their electrical characteristics. The 4× OD minimum is crucial for preventing signal degradation, but many manufacturers recommend larger radii for optimal performance. Excessive bending can cause impedance mismatches, crosstalk, and return loss that degrades network performance.
How to Calculate Bending Radius: A Simple Example
Let's work through a practical example to illustrate how these calculations work in real-world scenarios.
Consider an unarmoured 3-core power cable with an outer diameter (OD) of 20mm. This might be a typical cable used for motor connections or general power distribution in an industrial facility.
Step 1: Identify the cable type and factor
Cable type: Unarmoured power cable
Bending factor: 6× OD
Step 2: Calculate the minimum bending radius
Minimum Bending Radius = 6 × 20mm = 120mm
Step 3: Determine the bending diameter
Bending Diameter = 2 × 120mm = 240mm
What this means practically: This cable cannot be bent around any corner, conduit bend, or cable tray turn that has a radius smaller than 120mm. When planning the installation, you need to ensure that any 90-degree turns use conduit elbows or cable tray sections with at least a 120mm radius.
For installation in a cable tray, this means the cable needs at least 240mm of width to make a complete 180-degree turn. When routing through conduits, the conduit bends must accommodate this radius, which often requires larger conduit sizes or specialized long-radius elbows.
If you're installing this cable in a tight electrical panel, you might need to plan a path that approaches the connection point from a direction that allows for the proper bending radius, rather than forcing a sharp turn that violates the cable's physical limits.
How to Bend Cables Safely: Best Practices
Proper cable bending isn't just about knowing the numbers—it's about implementing practical techniques that protect your investment and ensure long-term reliability.
Never Exceed the Radius—Even Temporarily
One of the most common mistakes is temporarily over-bending cables during installation with the intention of relieving the stress afterward. Unfortunately, the damage from over-bending occurs immediately and cannot be reversed. Once the insulation cracks or conductors deform, the damage is permanent. Always maintain the proper radius throughout the entire installation process.
Use Proper Tools and Techniques
Professional installers rely on specialized tools to maintain proper bending radii. Cable rollers guide cables around corners while maintaining the correct radius. Bending jigs provide templates for consistent bends. Conduit elbows with appropriate radii eliminate guesswork. For cable tray installations, use tray sections specifically designed for direction changes with adequate radius.
Environmental Considerations
Temperature significantly affects cable flexibility. Cold temperatures make insulation materials brittle and require larger bending radii to prevent cracking. When installing cables in cold conditions or unheated spaces, increase the bending radius by 25-50% compared to room temperature requirements. Some manufacturers provide temperature correction factors in their technical documentation.
Avoid Repeated Flexing
While a cable might survive one bend at its minimum radius, repeated flexing at this limit will cause fatigue failure. For applications requiring movement, select cables specifically designed for dynamic applications and maintain bending radii well above the minimum requirements. Consider the total number of flex cycles expected over the cable's lifetime.
Plan Cable Routes Carefully
Good cable management begins with proper planning. Design cable routes that naturally accommodate proper bending radii rather than forcing cables into inappropriate paths. This might mean using larger conduits, additional pull boxes, or alternative routing paths that seem less direct but ultimately provide better long-term reliability.
International Standards to Know
Professional cable installations must comply with recognized standards that establish minimum requirements for safety and performance. These standards represent decades of experience and testing to determine safe practices.
IEC 60204-1: Safety of Machinery — Electrical Equipment of Machines
This international standard covers electrical equipment used in machines and establishes requirements for cable installation, including minimum bending radii. It's particularly relevant for industrial applications where cables are integrated into machinery systems.
IEC 60502-1/2: Power Cables with Extruded Insulation
These standards specifically address power cables with extruded insulation (like XLPE and EPR) and provide detailed requirements for installation, including bending radius guidelines. They're essential references for power cable installations in commercial and industrial settings.
IEEE Std 525: IEEE Guide for the Design and Installation of Cable Systems
This comprehensive guide covers cable system design and installation practices, including detailed information about bending radii for different cable types. It's particularly valuable for large-scale installations and provides practical guidance for engineers and installers.
NEC (NFPA 70): National Electrical Code
In the United States, the National Electrical Code establishes minimum requirements for electrical installations, including cable bending radii in conduit systems. These requirements are legally enforceable in most jurisdictions and represent the minimum acceptable practices.
Regional and Local Codes
Many countries and regions have additional requirements that may be more stringent than international standards. Always verify local code requirements before beginning any installation.
Who Needs to Care?
Understanding safe cable bending radius is crucial for several professional groups, each with specific concerns and applications.
Electrical Contractors
Electrical contractors are on the front lines of cable installation and bear direct responsibility for following proper bending practices. They need to understand requirements for different cable types, plan installations that accommodate proper radii, and educate their crews about the importance of these practices. The cost of callbacks due to cable failures far exceeds the effort required to do the job right the first time.
Port Crane Cable Installers
Port crane applications present unique challenges with heavy-duty power cables that must withstand constant movement, environmental exposure, and mechanical stress. These installers work with some of the most demanding cable applications and must understand both static and dynamic bending requirements. The consequences of cable failure in these applications can shut down entire port operations.
Data Center Designers
Modern data centers contain thousands of cables in high-density environments. Designers must plan cable management systems that accommodate proper bending radii while maximizing space efficiency. The high cost of downtime in data centers makes proper cable management a critical investment in reliability.
Engineers Designing Tray Systems
Engineers who design cable tray systems must understand bending radius requirements to specify appropriate tray sections, elbows, and transitions. Their designs must accommodate the largest cables expected while providing practical installation paths for smaller cables.
Procurement Professionals
Buyers who specify cable requirements need to understand how bending radius affects cable selection and installation costs. A cable with a smaller bending radius might have a higher initial cost but could save money in installation by requiring smaller conduits or tray systems.
Common Installation Q&A
Q: What if I need to make a turn that's tighter than the recommended bending radius? A: Never compromise on bending radius. Instead, consider alternative routing paths, use smaller cables if possible, or modify the installation design to accommodate the proper radius. The short-term inconvenience of redesigning the route is minimal compared to the long-term costs of cable failure.
Q: Can I temporarily over-bend a cable during installation if I relieve the stress afterward? A: No. Damage from over-bending occurs immediately and cannot be reversed. The cable must maintain its proper bending radius throughout the entire installation process, not just in its final position.
Q: How do I measure the bending radius in an existing installation? A: Use a radius gauge or flexible curve ruler to measure the actual radius of bends. Compare this to the cable manufacturer's specifications. If you find violations, plan for cable replacement during the next maintenance cycle.
Q: Are there different requirements for vertical versus horizontal bends? A: Generally, bending radius requirements are the same regardless of orientation. However, vertical installations may have additional considerations related to cable support and the weight of the cable itself.
Q: What should I do if the cable manufacturer's specifications differ from code requirements? A: Always follow the more stringent requirement. If the manufacturer specifies a larger bending radius than the code minimum, use the manufacturer's specification. The manufacturer understands their specific cable construction better than generic code requirements.
Q: How do I handle bending radius requirements in retrofit situations where space is limited? A: Retrofit situations often require creative solutions. Consider using more flexible cable types, alternative routing paths, or specialized cable management hardware designed for tight spaces. Sometimes the solution involves using multiple smaller cables instead of one large cable.
Conclusion: Bend It Right, or Pay the Price
The concept of safe cable bending radius might seem like a technical detail, but it's actually fundamental to electrical system reliability, safety, and cost-effectiveness. Every cable installation decision made today will impact system performance for decades to come.
The risks of ignoring proper bending practices are clear: mechanical damage leads to electrical failures, which cause system downtime, safety hazards, and expensive replacements. The immediate convenience of forcing a cable into a tight space is quickly forgotten, but the consequences of that decision can persist throughout the system's operational life.
Conversely, the benefits of proper cable management extend far beyond avoiding failures. Systems designed with proper bending radii are easier to maintain, more reliable, and often more efficient. They project professionalism and competence, which can be valuable for contractors building their reputation and engineers designing systems that will be evaluated for years to come.
The investment in proper cable management pays dividends in reduced maintenance costs, improved system reliability, and enhanced safety. Whether you're installing a single motor connection or designing a complex data center, the principles remain the same: respect the physical limits of your materials, plan your installations carefully, and always check manufacturer specifications for cable-specific requirements.
Remember that cable bending radius requirements exist for good reasons, backed by decades of experience and extensive testing. These aren't arbitrary restrictions—they're essential guidelines that protect your investment and ensure the safety and reliability of electrical systems. When in doubt, err on the side of caution and always consult the manufacturer's technical documentation for specialized cables or challenging applications.
The next time you're planning a cable installation, remember that taking the time to calculate and accommodate proper bending radii isn't just good practice—it's an investment in the long-term success of your electrical system. Bend it right, or pay the price later.
How to Reach Us
Get in Touch
SiteMap
Product Catalogue
Reeling Cable
Festoon Cable
Shore Power Cable
Hybrid Cable
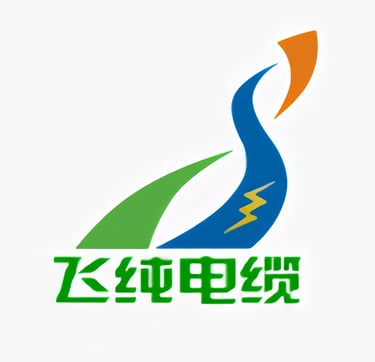
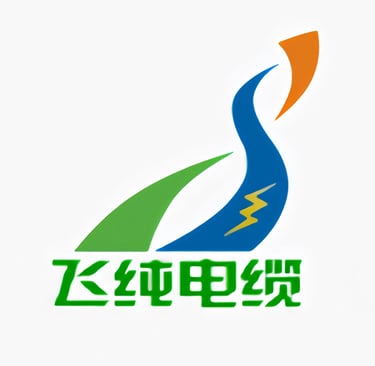
Copyright © 2025 Feichun Australia. All rights reserved.