What Is a VFD and a VFD Cable, and What Makes VFD Cables Unique?
What is a VFD and why do you need a special VFD cable? Discover the working principle of variable frequency drives, the unique challenges they introduce—like EMI, voltage spikes, and harmonics—and how VFD cables are designed to handle these stresses to ensure motor efficiency, safety, and longevity.
hongjing.Wang@Feichun
7/17/20258 min read
Why Ask About VFD and VFD Cables?
In today's industrial landscape, energy efficiency and precise motor control have become paramount concerns for engineers and facility managers. From manufacturing plants to port facilities, the demand for intelligent motor control systems continues to grow as industries seek to optimize energy consumption while maintaining operational reliability. At the heart of these systems lies the Variable Frequency Drive (VFD), a sophisticated electronic device that has revolutionized how we control AC motors.
However, the advanced capabilities of VFDs come with unique electrical challenges that standard power cables simply cannot handle. Understanding what is the purpose of a VFD cable in motor control becomes crucial when implementing these systems. The cable connecting a VFD to its motor is not just a conduit for power—it's a critical component that must withstand electrical stresses, manage electromagnetic interference, and ensure system longevity. This makes the selection of appropriate VFD cables as important as choosing the drive itself.
Diagram of VFD System:


What is a VFD (Variable Frequency Drive)?
A VFD, also known as a Variable Speed Drive (VSD), Adjustable Frequency Drive (AFD), or AC drive, is an electronic device that controls the speed, torque, and direction of AC electric motors. The fundamental principle behind VFD operation involves a three-stage process that transforms fixed-frequency AC power into variable-frequency output.
The basic working principle follows this sequence: incoming AC voltage is first converted to DC voltage through a rectifier stage, typically using diodes or Silicon Controlled Rectifiers (SCRs). This rectified power, originally at 460 Volts AC and 60 Hz, becomes approximately 650 Volts DC. The second stage involves a DC bus—essentially a large capacitor that stores and filters this DC voltage, acting as an energy reservoir for the final stage.
The third component, the inverter, converts the DC voltage back to AC using fast-switching devices like Insulated Gate Bipolar Transistors (IGBTs). These devices can switch at frequencies up to 20,000 Hz, creating Pulse Width Modulation (PWM) signals that approximate sinusoidal waveforms at the desired frequency.
Motor speed control is achieved through frequency variation, following the relationship: Ns = (120 × f) / P, where Ns represents synchronous speed in RPM, f is the supply frequency in Hz, and P is the number of motor poles. By adjusting the output frequency, engineers can precisely control motor speed to match load requirements, resulting in significant energy savings and improved process control.
What is a VFD Cable?
A VFD cable is a specially engineered electrical cable designed to connect Variable Frequency Drives to AC motors. Unlike standard power cables, these specialized cables are constructed to handle the unique electrical phenomena generated by VFD systems, including high-frequency switching, voltage transients, and electromagnetic interference.
The primary role of a VFD cable extends beyond simple power transmission. It must maintain signal integrity while managing the electrical stresses inherent in VFD applications. Why does a VFD system need a special cable? The answer lies in the complex electrical environment created by high-speed switching operations.
When improper cables are used in VFD applications, several critical issues arise. Insulation failure occurs when standard cables cannot withstand the voltage spikes generated by PWM switching. EMI issues develop as unshielded cables radiate electromagnetic energy, interfering with nearby control systems. Additionally, impedance mismatches between the cable and motor create reflections that can double the voltage at motor terminals, leading to premature equipment failure.


Voltage Spike Waveforms with and without VFD Cable Shielding:
Why VFD Applications Demand Special Cables?
The demanding electrical environment of VFD systems creates several challenges that require specialized cable solutions. High-frequency PWM switching, operating at frequencies up to 20kHz, generates rapid voltage transitions that stress cable insulation. These fast rise times, combined with the cable's electrical characteristics, can produce voltage spikes exceeding 2000V on long cable runs—far beyond what standard cables can safely handle.
Harmonics represent another significant challenge in VFD applications. The switching action of the inverter creates harmonic frequencies—multiples of the fundamental frequency. Common harmonics include the 5th (300 Hz), 7th (420 Hz), 11th (660 Hz), and 13th (780 Hz) when the fundamental frequency is 60 Hz. These harmonics generate additional heat in both the cable and motor, while also creating electromagnetic interference that can disrupt nearby electronic equipment.
Reflections and voltage doubling occur when electrical pulses encounter impedance mismatches between the cable and motor. When a pulse reaches the motor terminals, the impedance difference causes partial reflection back toward the drive. At certain cable lengths, these reflected waves can combine with incoming pulses, effectively doubling the voltage and current at specific points along the cable. This phenomenon creates localized stress points that can lead to insulation breakdown and cable failure.
Inrush current during motor startup presents additional challenges. Motors can draw up to six times their full load current during startup, requiring cables with adequate conductor sizing to prevent voltage drop and excessive heating.
Key Characteristics of a High-Quality VFD Cable
High-quality VFD cables incorporate several specialized features designed to address the unique challenges of variable frequency drive applications:
Low Capacitance Construction: Reduces voltage reflections and minimizes power loss by limiting capacitive coupling between conductors. This feature is crucial for maintaining system efficiency and preventing voltage spikes at motor terminals.
XLPE/EPR Insulation: Cross-linked polyethylene (XLPE) or Ethylene Propylene Rubber (EPR) insulation provides superior dielectric strength to withstand high-frequency voltage spikes and rapid voltage changes characteristic of PWM operation.
Copper Shielding (Braid/Foil): Comprehensive shielding systems, typically combining copper braid and aluminum foil, prevent EMI radiation and protect sensitive control circuits from interference. This shielding is essential for maintaining electromagnetic compatibility in industrial environments.
Symmetrical Ground Conductors: Properly sized and positioned ground conductors help reduce common-mode noise and prevent bearing currents that can damage motor bearings over time. This symmetrical design ensures balanced current flow and minimizes circulating currents.
Robust Outer Jacket: Durable outer jackets made from materials like Thermoplastic Elastomer (TPE) or Chlorinated Polyethylene (CPE) provide resistance to harsh environmental conditions, including chemicals, UV exposure, oils, and mechanical abrasion.


Cable Cross-section Highlighting Insulation, Shielding, Grounding:
Impedance Matching and Reflections: Why It Matters
Understanding impedance matching is crucial for VFD system design. The reflection equation Vr = Vi × (Zm - Zc) / (Zm + Zc) demonstrates how impedance mismatches between the cable (Zc) and motor (Zm) create reflected voltages (Vr) from incident voltages (Vi).
When impedances are mismatched, substantial voltage amplification occurs at motor terminals, potentially doubling the applied voltage. This reflected energy not only represents wasted power but also creates stress conditions that can cause premature insulation breakdown in motor windings.
Engineers must carefully consider impedance matching when designing VFD systems. Proper cable selection involves matching the cable's characteristic impedance to the motor's input impedance as closely as possible. This approach maximizes power transfer efficiency while minimizing harmful reflections, particularly important in long cable runs where reflection effects are amplified.
How to Choose the Right VFD Cable
Selecting appropriate VFD cables requires careful consideration of several critical factors:
Current Rating: The cable must handle the motor's full load current plus any anticipated overload conditions. Proper current rating ensures safe operation without excessive heating or voltage drop.
Voltage Rating: Cable voltage rating should exceed the system voltage with appropriate safety margins. For example, a 460V AC system typically requires cables rated for 600V or higher to accommodate voltage spikes.
Temperature Rating: Installation environment dictates temperature requirements. Cables must maintain their electrical and mechanical properties across the expected temperature range, including heat generated by harmonics and switching losses.
EMI Cable Shielding Effectiveness: The shielding system must provide adequate protection against electromagnetic interference while maintaining flexibility for installation. Shield effectiveness ratings help quantify a cable's ability to contain EMI.
Compliance Standards: Adherence to relevant standards ensures safety and performance. Key standards include UL 2277 for flexible motor supply cables, IEC 60502 for power cables with extruded insulation, and IEEE 515 for industrial cable installation practices.
Applications of VFD Cables Across Industries
VFD cables find application across diverse industrial sectors, each with specific requirements and challenges:
HVAC Systems: Building automation relies heavily on VFD-controlled fans, pumps, and compressors. How to reduce EMI and voltage spikes in VFD installations becomes particularly important in buildings with sensitive electronic equipment.
Port and Maritime Operations: Port cranes, ship unloaders, and container handling equipment represent some of the most demanding applications for VFD cables. These systems require robust cables capable of withstanding harsh marine environments while maintaining reliability under heavy load conditions. The growing automation of port facilities and the trend toward larger, more efficient cargo handling equipment continues to drive demand for high-performance VFD cables in this sector.
Water Treatment Plants: Pump control systems in water treatment facilities require reliable VFD cables to ensure continuous operation of critical infrastructure. The combination of moisture exposure and the need for precise flow control makes proper cable selection essential.
Industrial Automation: Manufacturing systems increasingly rely on VFD-controlled motors for conveyor systems, robotics, and processing equipment. The features of low-capacity VFD cables become particularly valuable in these applications where multiple drives operate in close proximity.
Mining and Heavy Industry: Harsh operating conditions in mining applications demand the best cables for variable frequency drive applications, with emphasis on durability and resistance to environmental extremes.


Illustration of Standing Wave/Reflection Concept:
Future Demand for VFD Cables in Port Markets
The port industry is experiencing unprecedented growth in automation and electrification, driving increased demand for sophisticated VFD cable solutions. Modern port facilities are investing heavily in automated container handling systems, electric ship-to-shore cranes, and intelligent cargo management systems—all requiring reliable VFD cable infrastructure.
Several factors contribute to this growing demand. Environmental regulations are pushing ports toward cleaner, more efficient operations, making VFD-controlled electric systems increasingly attractive compared to traditional diesel-powered equipment. The trend toward larger container ships requires more powerful, precise crane systems that depend on advanced VFD technology.
Additionally, the digitalization of port operations creates new requirements for EMI-resistant cables that can maintain signal integrity in increasingly complex electromagnetic environments. As ports integrate IoT sensors, wireless communication systems, and automated guidance systems, the need for properly shielded VFD cables becomes even more critical.
The expansion of global trade and the development of new port facilities, particularly in emerging markets, further drives demand for high-quality VFD cables. These installations require cables that can perform reliably in diverse climate conditions while supporting the latest automation technologies.
Conclusion: Why VFD Cables Are a Must, Not an Option
VFD cables represent essential components in modern industrial motor control systems, not optional upgrades. The unique electrical challenges posed by Variable Frequency Drives—including high-frequency switching, voltage spikes, harmonics, and electromagnetic interference—require specialized cable solutions that standard power cables simply cannot provide.
Proper VFD cable selection ensures electrical stability, reduces motor wear, and enhances overall system lifespan. The investment in quality VFD cables pays dividends through reduced maintenance costs, improved system reliability, and prevention of costly equipment failures.
As industries continue to embrace automation and energy efficiency, the importance of proper VFD cable specification will only grow. Engineers and facility managers who understand the critical role of these specialized cables will be better positioned to design and maintain reliable, efficient motor control systems.
The key to successful VFD installations lies in recognizing that the cable is not merely a connection between the drive and motor—it's an integral component of the system that must be properly sized, shielded, and specified to avoid unexpected downtime and ensure long-term operational success. In an era where system reliability and efficiency are paramount, VFD cables truly represent a necessity, not a luxury.
How to Reach Us
Get in Touch
SiteMap
Product Catalogue
Reeling Cable
Festoon Cable
Shore Power Cable
Hybrid Cable
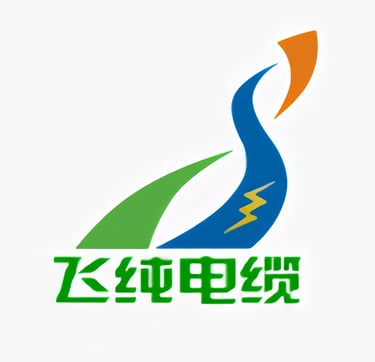
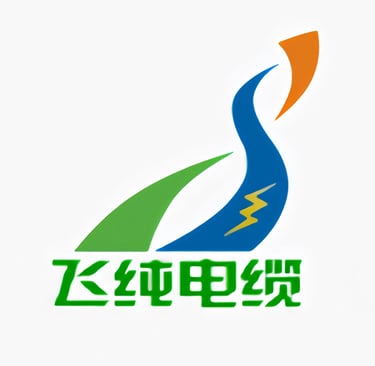
Copyright © 2025 Feichun Australia. All rights reserved.