What Is PUR Cable? Key Advantages and Applications in Modern Port Operations
Discover what PUR cables are, their superior mechanical and chemical resistance, and why they are the preferred choice for dynamic industrial environments like robotics, cable reels, and port automation systems.
hongjing.Wang@Feichun
7/9/202510 min read
Introduction
Modern industrial and port equipment operate in increasingly demanding environments where electrical cables must endure extreme conditions that would quickly destroy conventional wiring systems. From the salt-laden atmosphere of busy shipping terminals to the constant flexing motion of automated container handling equipment, today's industrial cables face unprecedented challenges. Port facilities, in particular, represent some of the most demanding environments for cable systems, where equipment must operate continuously in corrosive marine atmospheres while withstanding millions of mechanical cycles.
Traditional cable materials such as PVC and rubber compounds often fail prematurely in these harsh conditions, leading to costly downtime, safety hazards, and expensive maintenance cycles. The economic impact of cable failure in port operations can be staggering, with a single crane breakdown potentially costing thousands of dollars per hour in lost productivity. This reality has driven the development of advanced cable technologies that can reliably perform in these challenging environments.
The goal of this comprehensive guide is to clarify the nature and advantages of polyurethane (PUR) cables, providing engineers, maintenance professionals, and procurement specialists with the knowledge needed to make informed decisions about cable selection. By understanding the unique properties of PUR cables and their specific advantages in port and industrial applications, professionals can significantly improve system reliability while reducing long-term operating costs.
What is PUR Cable?
PUR cable represents a revolutionary advancement in cable technology, defined as a high-performance cable system that utilizes polyurethane as its outer sheath material. This classification places PUR cables within the thermoplastic elastomer (TPE-U) family, a sophisticated material category that combines the processing advantages of thermoplastics with the performance characteristics of elastomers.
Under the VDE (Verband der Elektrotechnik) classification system, PUR cables are designated with the code 11Y, which specifically identifies polyurethane-sheathed cables in European standards. In industry terminology, these cables are commonly referred to by several names including PUR cable, PU cable, and polyurethane cable, though all refer to the same fundamental technology.
The development of PUR cable technology represents decades of materials science research focused on overcoming the limitations of traditional cable materials. Unlike conventional cables that rely on rubber compounds or basic thermoplastics, PUR cables leverage the unique molecular structure of polyurethane to deliver unprecedented performance in demanding applications.
What distinguishes PUR cables from conventional alternatives is their ability to maintain flexibility and mechanical integrity under conditions that would cause traditional cables to fail. This breakthrough has made PUR cables the preferred choice for applications ranging from robotic systems to port automation equipment, where reliability is paramount and failure is not an option.
Chemical Composition and Structure
The exceptional performance of PUR cables stems from their sophisticated chemical composition and engineered structure. At the molecular level, PUR cables utilize polyurethane polymers that can be formulated using either polyether-based or polyester-based chemistries, each offering distinct performance advantages.
Polyether-based polyurethanes provide superior hydrolysis resistance, making them ideal for marine environments and applications involving exposure to moisture. These formulations maintain their properties even when exposed to water and humidity over extended periods, a critical advantage in port applications where cables may be exposed to salt spray and high humidity conditions.
Polyester-based polyurethanes, conversely, offer enhanced mechanical properties and superior chemical resistance, making them suitable for industrial environments where exposure to oils, solvents, and aggressive chemicals is common. These formulations provide excellent resistance to swelling and degradation when exposed to petroleum-based products and industrial chemicals.
The thermoplastic nature of polyurethane represents a fundamental advantage over traditional rubber-based cable materials. Unlike rubber compounds that require vulcanization or chemical cross-linking, polyurethane achieves its elastomeric properties through physical cross-linking mechanisms. This means that PUR materials can be melted and reprocessed without losing their fundamental properties, offering significant advantages in manufacturing efficiency and end-of-life recyclability.
The cable construction typically features multi-strand copper conductors designed to maintain electrical continuity during continuous flexing operations. These conductors are surrounded by insulation materials such as PVC (polyvinyl chloride) or XLPE (cross-linked polyethylene), selected based on the specific electrical requirements and environmental conditions of the application.
The polyurethane sheath serves as the primary protective barrier, providing mechanical strength, chemical resistance, and environmental protection. This multi-layer approach ensures that each component is optimized for its specific function while contributing to the overall performance of the cable system.
Main Performance Characteristics
The remarkable performance characteristics of PUR cables make them ideally suited for the demanding conditions encountered in port and industrial environments.
Mechanical Properties: PUR cables demonstrate exceptional mechanical strength, with tensile strengths typically ranging from 30 to 45 N/mm². This high tensile strength is particularly important in port applications where cables may be subjected to significant mechanical loads during crane operations or container handling. The outstanding tear and wear resistance of PUR cables provides protection against the abrasive conditions commonly encountered in industrial environments, while their superior impact resistance protects against mechanical damage during installation and operation.
Flexibility and Bending Life: Perhaps the most critical characteristic for port applications is the exceptional flexibility and bending life of PUR cables. These cables can achieve bending radii as small as 4 times the cable diameter while maintaining full electrical and mechanical integrity. More importantly, PUR cables can withstand millions of bending cycles without degradation, making them ideal for applications such as container crane trolley systems, ship-to-shore cranes, and automated guided vehicles (AGVs) that operate continuously in port environments.
Chemical and Oil Resistance: Port environments expose cables to a wide range of chemicals and contaminants, including hydraulic fluids, diesel fuel, saltwater, and various industrial solvents. PUR cables provide exceptional resistance to these substances, maintaining their properties even after prolonged exposure. This chemical resistance is particularly valuable in port applications where cables may be exposed to fuel spills, hydraulic fluid leaks, and other chemical contaminants that would quickly degrade conventional cables.
Temperature Performance: PUR cables typically operate effectively across a temperature range of -40°C to +90°C, with specialized formulations extending the upper limit to +125°C. This wide temperature range is essential for port operations that continue in extreme weather conditions, from the freezing temperatures of northern ports to the extreme heat of equatorial regions. The excellent low-temperature flexibility ensures reliable operation even in arctic conditions where conventional cables would become brittle and fail.
Environmental Adaptability: The marine environment presents unique challenges that PUR cables are specifically designed to address. UV resistance protects against degradation from intense sunlight, while ozone resistance prevents cracking and deterioration in industrial atmospheres. The moisture resistance of PUR cables is particularly important in port environments where high humidity and salt spray are constant concerns. Many PUR formulations also provide antimicrobial properties, preventing the growth of bacteria and fungi that could compromise cable integrity in humid marine environments.
Safety Features: Advanced PUR cable formulations incorporate low-smoke, halogen-free compounds that meet stringent fire safety requirements. Self-extinguishing versions comply with flame retardant standards while maintaining environmental compatibility. These safety features are particularly important in port applications where fire safety is critical due to the presence of flammable cargo and the enclosed nature of many port structures.
Common PUR Cable Types
The versatility of PUR cable technology has led to the development of numerous specialized cable types, each optimized for specific port and industrial applications.
Drag Chain and Trailer Cables: These cables are specifically engineered for energy chain systems and continuous motion applications common in port automation. Available in both flat and round configurations, they feature optimized conductor layouts that minimize stress during constant flexing. In port applications, these cables are essential for container crane trolley systems, automated stacking cranes, and ship-to-shore crane operations where cables must travel long distances while maintaining electrical integrity.
Robot and Automation Control Cables: Modern port operations rely heavily on automated systems that require sophisticated control cables. These shielded multi-core cables provide superior electromagnetic interference (EMI) protection, ensuring reliable signal transmission in the electrically noisy environment of port operations. The shielding is essential for maintaining communication integrity between control systems and automated equipment such as AGVs, robotic container handling systems, and automated gate systems.
Marine and Outdoor Power/Communication Cables: These specialized cables feature enhanced UV protection and salt spray resistance, making them ideal for the harsh marine environment of port operations. The formulations used in these cables are specifically designed to resist the corrosive effects of saltwater while providing long-term reliability in coastal installations. These cables are essential for pier lighting systems, communication networks, and power distribution in marine terminals.
Stage Lighting and Audio Connection Cables: While not traditionally associated with port operations, these highly flexible cables find applications in port facilities for temporary lighting systems, public address systems, and event management during special operations or ceremonies.
Medical and Food-Grade Cables: These specialized cables meet strict hygiene requirements and find application in port facilities that handle food products or require clean environments for cargo inspection and processing.

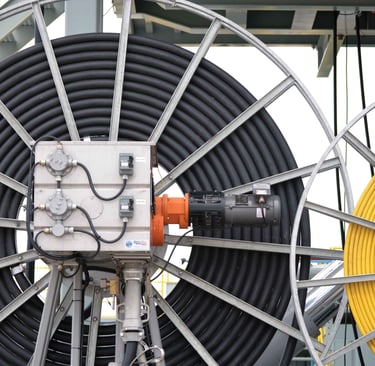
Typical Application Scenarios
The unique properties of PUR cables make them essential for numerous demanding applications in port and industrial environments.
Port Crane Systems: Container cranes represent one of the most demanding applications for PUR cables. Ship-to-shore cranes require cables that can withstand millions of bending cycles as they move containers between ships and terminal storage areas. The cables must maintain electrical integrity while operating in salt spray conditions and extreme temperatures. PUR cables provide the flexibility needed for the complex cable management systems used in these cranes, including festoon systems and cable reels that manage hundreds of meters of cable during crane operations.
Automated Stacking Cranes: Rubber-tired gantry cranes (RTGs) and rail-mounted gantry cranes (RMGs) used in container yards require cables that can withstand the constant motion and vibration associated with container handling operations. PUR cables provide the durability and flexibility needed for these applications, where cable failure can result in significant operational disruptions and safety hazards.
Ship-to-Shore Cable Systems: The connection between ships and shore facilities requires cables that can withstand the constant motion of vessels due to tides and weather conditions. PUR cables provide the flexibility and durability needed for these applications, maintaining electrical continuity despite the dynamic nature of ship mooring systems.
Automated Guided Vehicles (AGVs): Modern port terminals increasingly rely on AGVs for container transport between different areas of the facility. These vehicles require flexible cables that can withstand the constant starting, stopping, and turning motions while maintaining reliable communication with central control systems. PUR cables provide the flexibility and durability needed for these applications.
Port Lighting and Communication Systems: Port facilities require extensive lighting and communication networks that must operate reliably in harsh marine environments. PUR cables provide the environmental resistance needed for these permanent installations, maintaining performance despite exposure to salt spray, UV radiation, and temperature extremes.
Cargo Handling Equipment: Various types of cargo handling equipment, including conveyor systems, loading bridges, and specialized cargo handling machinery, require cables that can withstand the mechanical stresses and environmental conditions encountered in port operations.

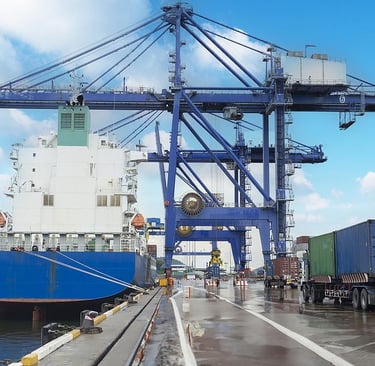

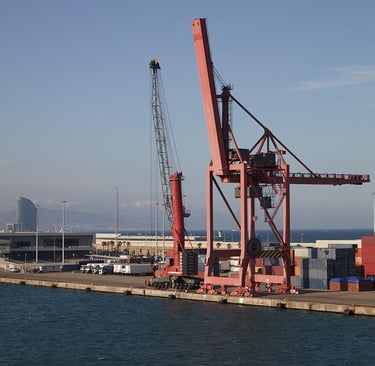
Selection Points and Installation Precautions
Proper selection and installation of PUR cables in port applications requires careful consideration of multiple factors to ensure optimal performance and longevity.
Environmental Conditions Assessment: Port environments present unique challenges that must be carefully evaluated during cable selection. Salt spray conditions require cables with enhanced corrosion resistance and appropriate sealing systems. UV exposure levels must be assessed to ensure adequate UV stabilization in the cable formulation. Temperature extremes, both seasonal and operational, must be considered to ensure the selected cable can maintain performance across the expected temperature range.
Mechanical Load Calculation: Port applications often involve complex mechanical loading scenarios that require detailed analysis. Container crane operations involve not only bending cycles but also tension loads as cables support their own weight over long spans. The stroke length, operating speed, and acceleration rates of automated equipment must be carefully calculated to ensure the selected cable can withstand the mechanical stresses involved.
Chemical Exposure Assessment: Port environments expose cables to a wide range of chemicals, including hydraulic fluids, diesel fuel, cleaning solvents, and various cargo-related substances. Understanding the specific chemical exposure risks in each application is essential for selecting the appropriate PUR formulation.
Safety and Standards Compliance: Port operations are subject to stringent safety regulations that may require specific cable characteristics. Fire safety requirements may mandate low-smoke, halogen-free formulations, while electrical safety standards may require specific insulation properties. Compliance with international standards such as VDE, IEC, and maritime regulations must be verified during cable selection.
Installation Considerations: Proper installation is critical for maximizing PUR cable performance in port applications. Cable support systems must be designed to accommodate the expected range of motion while preventing excessive bending or tension. Minimum bending radii must be maintained throughout the installation, and proper strain relief must be provided at connection points. The harsh marine environment requires special attention to connection sealing and corrosion protection.
Maintenance and Inspection Requirements: Port cables require regular inspection and maintenance to ensure continued reliability. Understanding the specific maintenance requirements and inspection intervals for different cable types is essential for developing effective maintenance programs.
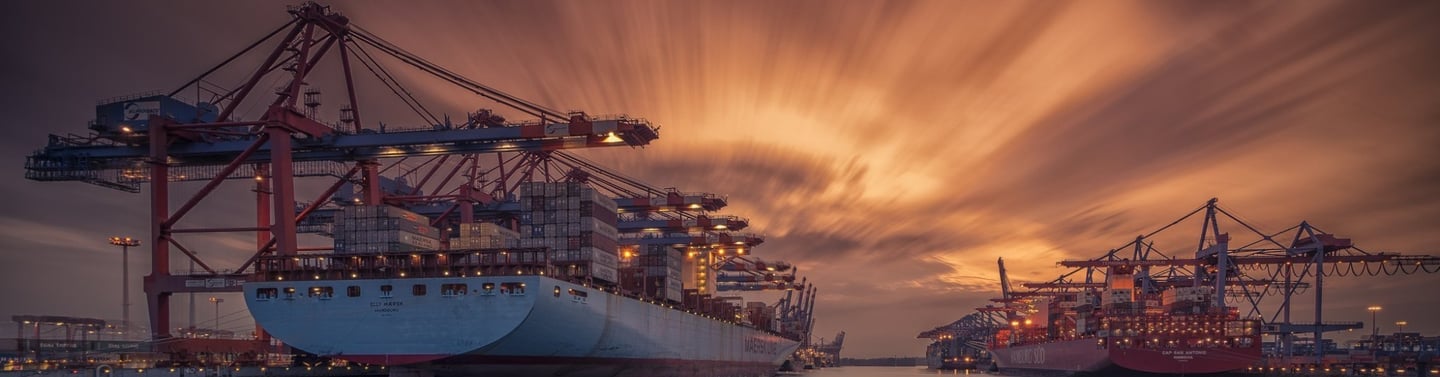
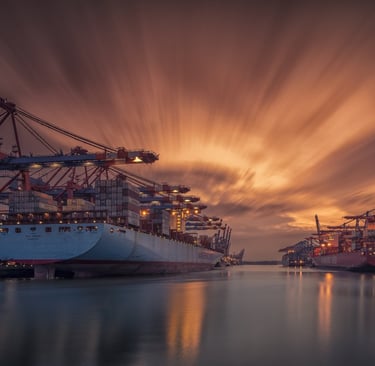
Future Development Trends
The evolution of PUR cable technology continues to advance, driven by the increasing demands of modern port operations and environmental consciousness.
Advanced Environmental Formulations: The development of new environmentally friendly PUR formulations represents a significant advancement in cable technology. Halogen-free flame retardant formulations provide enhanced fire safety without environmental impact, while high-temperature resistant materials extend the operating temperature range for specialized applications. These new formulations maintain the excellent mechanical and chemical properties of traditional PUR cables while meeting increasingly stringent environmental requirements.
Intelligent Cable Systems: The integration of sensors and monitoring systems into PUR cables represents a revolutionary advancement in cable technology. These intelligent cables can provide real-time monitoring of temperature, strain, electrical parameters, and even chemical exposure, enabling predictive maintenance and preventing failures before they occur. In port applications, intelligent cables could monitor the condition of crane systems, providing advance warning of potential cable failures and enabling scheduled maintenance during planned downtime.
Modular and Composite Systems: Future PUR cable designs are moving toward modular systems that integrate multiple functions in a single cable. This includes combining power transmission, data communication, hydraulic lines, and monitoring capabilities in optimized cable designs. For port applications, this could mean single cables that provide power, control signals, and hydraulic pressure to crane systems while monitoring their own condition and performance.
Enhanced Marine-Specific Formulations: As port operations become more sophisticated, specialized PUR formulations are being developed specifically for marine environments. These include enhanced salt spray resistance, improved UV stabilization, and specialized anti-fouling properties that prevent marine growth on submerged cables.
Sustainable and Recyclable Materials: The development of bio-based polyurethane formulations represents an important trend toward environmental sustainability. These materials maintain the performance characteristics of traditional PUR cables while reducing the environmental impact of cable manufacturing and disposal.
Conclusion
PUR cables represent a fundamental advancement in cable technology that has revolutionized the reliability and performance of electrical systems in port and industrial applications. The combination of exceptional flexibility, chemical resistance, environmental durability, and mechanical strength makes PUR cables the optimal choice for the demanding conditions encountered in modern port operations.
The specific advantages of PUR cables in port applications cannot be overstated. From the millions of bending cycles required in container crane operations to the harsh marine environment that degrades conventional cables, PUR cables provide the reliability and longevity that port operations demand. The ability to withstand salt spray, temperature extremes, and chemical exposure while maintaining electrical integrity makes PUR cables essential for modern port automation systems.
As port operations continue to evolve toward greater automation and efficiency, the role of high-performance cables becomes increasingly critical. The future development of intelligent cable systems, enhanced environmental formulations, and modular designs will further expand the capabilities of PUR cables, ensuring they remain the preferred choice for demanding port applications.
Organizations that invest in PUR cable technology will be better positioned to achieve reliable, efficient, and sustainable port operations in an increasingly competitive global shipping industry. The higher initial cost of PUR cables is quickly offset by their extended service life, reduced maintenance requirements, and improved system reliability, making them an essential component of modern port infrastructure.
How to Reach Us
Get in Touch
SiteMap
Product Catalogue
Reeling Cable
Festoon Cable
Shore Power Cable
Hybrid Cable
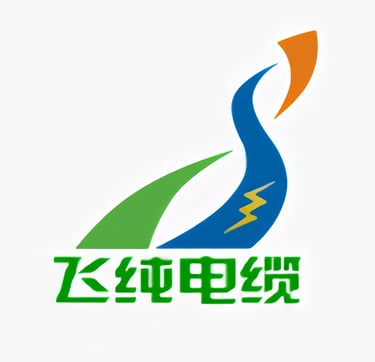
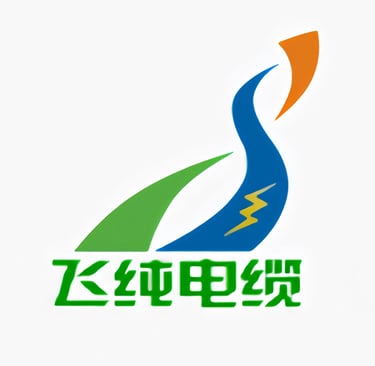
Copyright © 2025 Feichun Australia. All rights reserved.