What Is UV Cable? Materials, Applications, and Weather-Resistance Explained
What is UV-resistant cable? How to choose a cable suitable for outdoor use? This article explains its materials, standards and application cases in detail.
hongjing.Wang@Feichun
7/8/202521 min read
Introduction
In our increasingly connected world, electrical cables are the invisible arteries that power everything from city streetlights to remote industrial sensors. However, when these cables venture outside the protective confines of buildings, they face a formidable enemy: ultraviolet (UV) radiation from the sun. This invisible force, the same energy that causes sunburn on human skin, can systematically destroy conventional cables, causing them to crack, become brittle, and ultimately fail.
The aging problem of cables in outdoor environments is not merely an inconvenience—it represents a significant safety hazard and economic concern. When a cable's outer sheath degrades due to UV exposure, it can lead to insulation breakdown, electrical shorts, fires, and costly system downtime. In critical applications such as solar power installations, industrial monitoring systems, or maritime equipment, cable failure can result in substantial financial losses and safety risks.
This challenge has driven the development of UV-resistant cables, specialized electrical conductors designed to withstand prolonged exposure to sunlight without degrading. These cables incorporate advanced materials and additives that either absorb harmful UV radiation or prevent it from causing molecular damage to the cable's structure. Understanding why we need UV-resistant cables and how they work is essential for anyone involved in outdoor electrical installations, from residential solar panels to large-scale industrial facilities.
The importance of UV-resistant cables extends beyond mere durability. In an era where renewable energy systems, smart city infrastructure, and outdoor IoT devices are proliferating, the reliability of outdoor electrical connections has become paramount. A failed cable in a solar installation doesn't just mean lost power generation—it can cascade into system-wide failures that take weeks to repair and cost thousands of dollars in lost revenue.
Moreover, as climate change intensifies UV radiation levels in many regions, the challenge of protecting outdoor cables becomes even more critical. Traditional cables that might have lasted decades in moderate climates now face accelerated aging in increasingly harsh environmental conditions. This reality has made UV-resistant cables not just an option but a necessity for reliable outdoor electrical systems.
What is UV Cable? What Is a UV Cable?
A UV cable, also known as a UV-resistant or weatherproof cable, is a specialized electrical conductor engineered to resist degradation when exposed to ultraviolet radiation from sunlight. Unlike conventional cables that rely on basic insulation materials, UV cables incorporate advanced polymer formulations and protective additives specifically designed to withstand the photodegradation process that occurs when organic materials are exposed to UV radiation.
The fundamental difference between UV cables and ordinary cables lies in their molecular structure and composition. Standard electrical cables typically use basic PVC (polyvinyl chloride) or rubber compounds for their outer sheath, materials that are adequate for indoor use but vulnerable to UV breakdown. When exposed to sunlight, these materials undergo photodegradation, a process where UV photons break the chemical bonds in the polymer chains, causing the material to become brittle, discolored, and eventually crack.
UV cables combat this degradation through several sophisticated mechanisms. The most common approach involves incorporating UV stabilizers directly into the cable's sheath material. These stabilizers work as molecular shields, either absorbing UV radiation before it can damage the polymer or neutralizing the free radicals that UV exposure creates. Carbon black, one of the most effective UV stabilizers, is often added to cable compounds, giving many UV cables their characteristic black appearance while providing excellent protection against UV degradation.
The structural differences between UV cables and ordinary cables extend beyond just the outer sheath. UV cables often feature enhanced insulation systems that can maintain their electrical properties even after prolonged UV exposure. This might include cross-linked polyethylene (XLPE) insulation that provides superior electrical performance and thermal stability, or specialized rubber compounds that retain their flexibility and insulation properties despite UV stress.
Another critical distinction is the testing and validation process that UV cables undergo. While standard cables are tested primarily for electrical performance and basic mechanical properties, UV cables must pass rigorous accelerated aging tests that simulate years of outdoor exposure in compressed timeframes. These tests evaluate not only the cable's ability to resist UV degradation but also its performance under combined stresses of UV radiation, temperature cycling, and moisture exposure.
The construction of UV cables also typically involves more robust strain relief and connector systems designed to handle the thermal expansion and contraction that occurs in outdoor environments. The conductors themselves may be tinned or specially treated to resist corrosion from moisture that might penetrate a UV-damaged sheath, providing an additional layer of protection for long-term reliability.
Modern UV cables often incorporate multiple protection strategies simultaneously. For example, a high-quality UV cable might feature a dual-layer sheath system where an inner layer provides electrical insulation and mechanical protection, while an outer layer specifically formulated for UV resistance serves as the primary barrier against environmental degradation. This multi-layered approach ensures that even if the outer protection layer experiences some degradation, the inner systems continue to provide essential protection.


Main Materials Used of UV Cables
The superior performance of UV cables stems from carefully selected materials and additives that work together to resist ultraviolet degradation while maintaining electrical and mechanical properties. Understanding these materials provides insight into how UV cables achieve their remarkable longevity and reliability in outdoor applications.
Black PVC with Anti-UV Additives
Polyvinyl chloride (PVC) remains one of the most widely used materials for UV cable sheaths, but only when properly formulated with anti-UV additives. Standard PVC is notoriously susceptible to UV degradation, becoming brittle and discolored when exposed to sunlight. However, modern UV-resistant PVC compounds incorporate sophisticated additive systems that dramatically improve their outdoor performance.
The most effective anti-UV additives for PVC include UV absorbers such as benzotriazoles and benzophenones, which work by absorbing harmful UV radiation and converting it to harmless heat. These compounds are typically used in concentrations of 0.5% to 2% by weight, depending on the expected UV exposure intensity and desired service life. Additionally, hindered amine light stabilizers (HALS) are often incorporated to neutralize free radicals generated by UV exposure, providing long-term protection even after the UV absorbers are exhausted.
The addition of these stabilizers must be carefully balanced to avoid compromising other essential properties. Too much UV absorber can affect the PVC's flexibility and processability, while too little provides inadequate protection. Modern formulations often use synergistic combinations of multiple additives to achieve optimal performance across all critical parameters.
PE (Polyethylene) and HDPE (High-Density Polyethylene)
Polyethylene-based materials offer excellent base properties for UV cable applications, particularly in terms of electrical insulation and moisture resistance. PE and HDPE naturally possess better UV resistance than many other polymers, but they still require additives for extended outdoor exposure. The crystalline structure of HDPE provides inherent toughness and chemical resistance, making it particularly suitable for harsh outdoor environments.
UV-stabilized PE compounds typically incorporate carbon black as the primary UV stabilizer, often in concentrations of 2% to 4% by weight. Carbon black provides excellent UV protection by absorbing UV radiation across a broad spectrum, preventing it from penetrating into the polymer matrix. The fine particle size and dispersion quality of carbon black are critical factors in achieving optimal UV protection.
Advanced PE formulations may also include antioxidants to prevent thermal degradation and processing aids to improve manufacturing consistency. Some specialized PE compounds incorporate grafted UV stabilizers that are chemically bonded to the polymer chains, providing more permanent protection that cannot migrate or be lost over time.
TPE (Thermoplastic Elastomer)
Thermoplastic elastomers represent a newer class of materials that combine the processing advantages of thermoplastics with the flexibility and performance characteristics of rubber. TPE materials offer excellent flexibility across a wide temperature range, making them particularly suitable for applications where cables must remain flexible in cold weather or accommodate frequent movement.
UV-resistant TPE formulations typically employ multiple protection strategies. Primary UV stabilizers such as UV absorbers and HALS are incorporated into the base polymer, while secondary stabilizers such as antioxidants provide protection against thermal and oxidative degradation. The thermoplastic nature of TPE allows for more uniform distribution of these additives during processing, potentially providing more consistent UV protection throughout the cable sheath.
The flexibility of TPE materials is particularly valuable in applications such as portable equipment connections, robotic systems, and installations where cables must accommodate thermal expansion and contraction. However, TPE materials are generally more expensive than traditional PVC or PE, limiting their use to applications where their superior flexibility justifies the additional cost.
PUR (Polyurethane) – Exceptional Flexibility and UV Resistance
Polyurethane (PUR) cables represent the premium segment of UV-resistant cables, offering exceptional flexibility combined with outstanding UV resistance. PUR materials maintain their flexibility across an extremely wide temperature range, from -40°C to +90°C, making them ideal for demanding outdoor applications. The chemical structure of polyurethane provides inherent resistance to many forms of degradation, including UV, ozone, and chemical exposure.
Modern PUR formulations for UV cables incorporate advanced UV stabilizer systems that provide protection equivalent to or better than other materials while maintaining superior mechanical properties. The exceptional tear resistance and abrasion resistance of PUR make it particularly suitable for applications where cables may be subject to mechanical stress, such as portable equipment or installations in high-traffic areas.
PUR cables often feature enhanced conductor designs that complement the superior sheath materials. Fine-stranded conductors provide flexibility that matches the PUR sheath, while specialized insulation materials ensure that the entire cable system maintains its performance characteristics throughout its service life. The higher cost of PUR materials is justified in applications where cable failure would result in significant downtime or replacement costs.

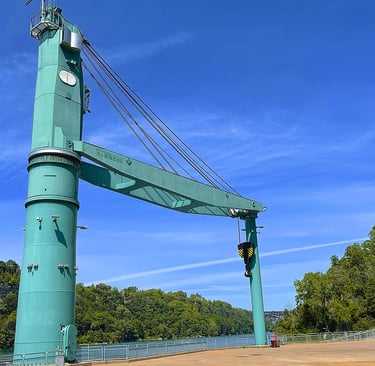
The Role of UV Stabilizers and Carbon Black
The effectiveness of UV cables depends heavily on the UV stabilizer systems incorporated into their materials. UV stabilizers work through several mechanisms, each addressing different aspects of the UV degradation process. Primary UV stabilizers, such as UV absorbers, work by absorbing harmful UV radiation before it can initiate degradation reactions. These compounds are typically aromatic molecules that can absorb UV energy and dissipate it as harmless heat.
Secondary UV stabilizers, including hindered amine light stabilizers (HALS), work by neutralizing free radicals generated during UV exposure. These compounds are particularly effective for long-term protection because they are regenerated during the stabilization process, providing continuing protection throughout the cable's service life. The combination of primary and secondary stabilizers often provides synergistic effects that exceed the protection available from either type alone.
Carbon black deserves special attention as perhaps the most effective and widely used UV stabilizer for cable applications. When properly dispersed in the polymer matrix, carbon black provides excellent UV protection by absorbing UV radiation across a broad spectrum. The effectiveness of carbon black depends on its particle size, surface area, and dispersion quality. Fine particle size and high surface area provide better UV absorption, while proper dispersion ensures uniform protection throughout the cable sheath.
Material Performance Comparison Under UV Irradiation
The relative performance of different UV cable materials depends on multiple factors, including the specific UV stabilizer system, the intensity and spectrum of UV exposure, and the presence of other environmental stresses such as temperature and moisture. Laboratory testing using accelerated aging methods provides valuable data for comparing material performance under controlled conditions.
PUR materials generally provide the longest service life under UV exposure, often exceeding 20 years in moderate climates. However, their higher cost limits their use to applications where their superior performance justifies the additional expense. TPE materials offer a good balance of performance and cost, with typical service lives of 10-15 years under normal outdoor conditions.
UV-stabilized PVC and PE materials provide adequate performance for many applications, with service lives of 5-10 years depending on the specific formulation and environmental conditions. The key to successful material selection is matching the performance characteristics and cost to the specific application requirements, considering factors such as expected service life, environmental conditions, and the consequences of cable failure.
Applicable Scenarios and Application Industries
UV cables find application across a vast array of industries and scenarios where electrical systems must operate reliably under direct sunlight exposure. Their versatility and reliability have made them indispensable components in modern infrastructure, from renewable energy installations to industrial automation systems.
Outdoor Lighting Systems
Municipal and commercial outdoor lighting represents one of the largest application areas for UV cables. Street lighting systems, parking lot illumination, and architectural lighting installations all require cables that can withstand decades of continuous UV exposure while maintaining electrical safety and reliability. The failure of lighting cables can create safety hazards and security concerns, making UV resistance a critical requirement.
Modern LED lighting systems have increased the importance of UV cable selection due to their longer expected service lives. While traditional lighting systems might be replaced every few years, LED installations are designed to operate for 15-20 years or more. This extended service life requires cables that can maintain their performance throughout the lighting system's operational lifetime.
Smart lighting systems add another layer of complexity, as they often require data cables in addition to power cables. UV-resistant data cables must maintain their signal integrity while resisting environmental degradation, requiring specialized materials and construction techniques. The integration of sensors, controllers, and communication systems in modern lighting installations has created demand for multi-conductor UV cables that can handle both power and data transmission.
Photovoltaic Solar Energy Systems
The solar energy industry represents perhaps the most demanding application for UV cables, as these systems are specifically designed to maximize sun exposure while operating for 25-30 years or more. Solar cables must not only resist UV degradation but also maintain their electrical properties under high temperatures and temperature cycling that occurs in solar installations.
Solar cables typically operate at DC voltages of 600V to 1500V, requiring insulation systems that can maintain their breakdown voltage throughout the cable's service life. The combination of high voltage, high temperature, and intense UV exposure creates particularly challenging conditions that require specialized cable designs and materials.
The expansion of floating solar installations has created new challenges for UV cable applications. These systems operate in environments where UV reflection from water surfaces can effectively double the UV exposure compared to land-based installations. Additionally, the constant motion and flexibility requirements of floating systems place additional mechanical demands on cable systems, requiring materials that can withstand both UV exposure and repeated flexing.
Large-scale solar installations often employ cable monitoring systems that can detect cable degradation before failure occurs. These systems rely on UV-resistant sensor cables and communication cables that must maintain their performance while exposed to the same environmental conditions as the power cables they monitor.
Industrial Equipment and Monitoring Systems
Industrial facilities increasingly rely on outdoor monitoring and control systems that require UV-resistant cables for reliable operation. These applications include environmental monitoring sensors, security cameras, industrial process controls, and automation systems that must operate in outdoor environments.
Petrochemical facilities present particularly challenging environments for UV cables, as they must resist not only UV degradation but also chemical exposure from various industrial processes. The combination of UV exposure, temperature extremes, and chemical exposure requires specialized cable designs that can withstand multiple degradation mechanisms simultaneously.
Mining operations often require UV cables for mobile equipment and outdoor installations in remote locations where cable failure can result in significant operational disruptions. The harsh environmental conditions typical of mining sites, including dust, moisture, and temperature extremes, combined with intense UV exposure, require cables with superior environmental resistance.
Coastal and Marine Environments
Coastal and marine environments present unique challenges for UV cable applications due to the combination of intense UV exposure, salt spray, and high humidity. The reflection of UV radiation from water surfaces can significantly increase the effective UV exposure compared to land-based installations, while salt spray can accelerate certain types of degradation.
Port and dock facilities rely heavily on UV cables for cargo handling equipment, lighting systems, and security installations. These cables must maintain their performance while exposed to marine conditions including salt spray, high humidity, and potentially corrosive atmospheres. The critical nature of port operations makes cable reliability essential for maintaining operational efficiency and safety.
Ship and offshore platform installations require UV cables that can withstand the most extreme marine conditions. These applications often involve cables that must maintain their performance while exposed to salt spray, UV radiation, and mechanical stresses from wave action and wind loading. The remote location of many offshore installations makes cable reliability particularly critical, as replacement and repair operations can be extremely costly and time-consuming.
Floating wind turbines represent an emerging application area that combines the challenges of marine UV exposure with the mechanical stresses of wind energy systems. These installations require cables that can maintain their performance while exposed to marine UV radiation, salt spray, and the constant motion of floating platforms.
Building Exterior and Rooftop Applications
Building exterior and rooftop electrical installations increasingly require UV-resistant cables for various applications including rooftop solar installations, building automation systems, and exterior lighting. Rooftop environments can be particularly challenging due to limited airflow, high temperatures from roof heat absorption, and intense UV exposure.
Building-integrated photovoltaic (BIPV) systems require UV cables that can maintain their appearance as well as their electrical performance, as these cables may be visible as part of the building's aesthetic design. This requires careful selection of materials and UV stabilizers that prevent discoloration while maintaining electrical performance.
Smart building systems often require UV cables for outdoor sensors, communication systems, and control equipment. These systems must maintain their performance while exposed to building exterior conditions, including UV radiation, temperature extremes, and weather exposure. The integration of these systems with building automation requires cables that can maintain their electrical and data transmission properties throughout the building's operational lifetime.
Agricultural and Irrigation Applications
Agricultural applications increasingly rely on UV cables for irrigation systems, livestock monitoring, and precision agriculture equipment. These applications often involve cables installed in remote locations where maintenance access is limited, making long-term reliability essential.
Solar-powered irrigation systems require UV cables that can operate reliably in rural environments while powering critical agricultural operations. The failure of irrigation cables can result in crop losses that far exceed the cost of the cables themselves, making reliability a critical economic factor.
Precision agriculture systems employ numerous sensors and monitoring devices that require UV-resistant cables for data transmission and power supply. These systems must operate reliably throughout growing seasons while exposed to outdoor conditions, requiring cables that can maintain their performance under various environmental stresses.
Livestock monitoring systems often require UV cables for outdoor installations including automated feeding systems, environmental controls, and security systems. These applications require cables that can maintain their performance while exposed to agricultural environments that may include dust, moisture, and chemical exposure from agricultural operations.
Technical Standards & Certification
The development and deployment of UV cables is governed by a comprehensive framework of technical standards and certifications that ensure safety, performance, and reliability across different applications and geographic regions. These standards provide the foundation for testing protocols, performance requirements, and quality assurance procedures that manufacturers and users rely upon.
International Standards Framework
The International Electrotechnical Commission (IEC) provides fundamental standards for UV cable testing and performance. IEC 60216 establishes procedures for determining the thermal endurance properties of electrical insulating materials, including testing protocols that evaluate long-term performance under elevated temperatures. This standard is particularly relevant for UV cables because UV exposure often occurs simultaneously with high temperatures in outdoor applications.
IEC 62930 specifically addresses cables for photovoltaic systems, establishing comprehensive requirements for UV resistance, temperature performance, and electrical characteristics. This standard has become the international benchmark for solar cable performance and is widely adopted by manufacturers and testing laboratories worldwide.
European Standards and Regulations
EN 50618 represents the European standard for electric cables used in photovoltaic systems, establishing specific requirements for UV resistance testing and performance criteria. This standard incorporates rigorous testing protocols that evaluate cable performance under accelerated aging conditions designed to simulate years of outdoor exposure.
The EN 50618 standard requires cables to demonstrate UV resistance according to HD 605/A1 testing protocols, which subject cables to controlled UV exposure while monitoring changes in electrical and mechanical properties. Cables must maintain their insulation resistance, dielectric strength, and mechanical properties after specified exposure periods to meet certification requirements.
The Construction Products Regulation (CPR) in Europe requires UV cables used in construction applications to meet specific fire performance requirements in addition to UV resistance. This regulation ensures that UV cables do not contribute to fire propagation in building applications while maintaining their environmental resistance properties.
North American Standards
In North America, UL (Underwriters Laboratories) standards govern UV cable testing and certification. UL 1581 provides comprehensive test methods for electrical wires and cables, including specific procedures for evaluating UV resistance and long-term aging performance. This standard establishes testing protocols that simulate outdoor exposure conditions and define acceptance criteria for various cable types.
UL 4703 specifically addresses photovoltaic wire and cable, establishing requirements for UV resistance, temperature performance, and electrical characteristics that are specifically relevant to solar applications. This standard has been widely adopted by the North American solar industry and provides the foundation for cable selection and installation requirements.
The National Electrical Code (NEC) provides installation requirements that complement the performance standards, ensuring that UV cables are properly installed and protected in electrical systems. These requirements address factors such as cable routing, support, and protection that are essential for long-term reliability.
UV Resistance Testing Protocols
ASTM G154 is an internationally-recognized test practice for exposing materials to UV light using fluorescent lamps. The test simulates the same outdoor conditions materials see from damaging UV energy, elevated temperatures, and the high time of wetness from outdoor moisture. This standard provides the foundation for accelerated aging tests that evaluate UV cable performance under controlled laboratory conditions.
The ASTM G154 standard outlines the procedures for using a fluorescent UV lamp apparatus to mimic the effects of sunlight on various materials. This test involves placing material samples inside a specialized chamber. The chamber is fitted with UV lamps that emit radiation in the UV-A and UV-B spectral ranges that are most relevant to outdoor degradation processes.
ASTM G154 specifies a standardized procedure for achieving consistent, repeatable findings across laboratories and industry, ensuring that UV resistance testing provides reliable data for comparing different cable materials and designs. The standard includes provisions for different exposure cycles, temperature conditions, and humidity levels that simulate various outdoor environments.
Testing protocols typically involve exposing cable samples to controlled UV radiation for specified periods, followed by evaluation of electrical and mechanical properties. Changes in insulation resistance, dielectric strength, tensile strength, and elongation are measured to assess the degree of UV-induced degradation. Cables must maintain their properties within specified limits to meet certification requirements.
Certification Bodies and Processes
Several internationally recognized certification bodies provide testing and certification services for UV cables. TÜV Rheinland, TÜV SÜD, and other European notified bodies provide comprehensive testing services that evaluate compliance with European standards including EN 50618 and related requirements.
Underwriters Laboratories (UL) provides certification services for North American markets, including comprehensive testing programs that evaluate UV resistance along with electrical safety and fire performance. UL certification is often required for cables used in commercial and utility-scale installations.
The certification process typically involves initial product evaluation, comprehensive testing according to applicable standards, and ongoing surveillance to ensure continued compliance. Manufacturers must demonstrate that their production processes consistently produce cables that meet certification requirements, often requiring implementation of quality management systems and regular audits.
Quality Assurance and Testing Verification
Quality assurance for UV cables involves multiple levels of testing and verification, from raw material acceptance testing to final product certification. Material suppliers must provide certificates of analysis that verify the UV stabilizer content and other critical properties of cable compounds.
Production testing typically includes routine electrical tests, dimensional verification, and periodic UV resistance testing to ensure consistent product quality. Many manufacturers employ statistical process control methods to monitor production consistency and identify potential quality issues before they affect product performance.
Third-party testing laboratories provide independent verification of cable performance, often conducting witness testing where customers or certification bodies observe testing procedures to ensure compliance with specified requirements. This independent verification provides confidence that certified cables will perform as expected in real-world applications.
Purchase Suggestions (How to Choose the Right UV Cable?)
Selecting the appropriate UV cable for a specific application requires careful consideration of environmental conditions, electrical requirements, regulatory compliance, and long-term cost factors. The decision-making process should be systematic and comprehensive, ensuring that the chosen cable will provide reliable performance throughout its expected service life.
Environmental Assessment and Material Selection
The first step in UV cable selection involves a thorough assessment of the environmental conditions where the cable will be installed. Geographic location significantly impacts UV exposure intensity, with tropical and desert regions experiencing much higher UV levels than temperate climates. Altitude also affects UV exposure, as atmospheric filtering decreases with elevation, resulting in more intense UV radiation at higher altitudes.
Temperature considerations are equally important, as UV exposure typically occurs simultaneously with elevated temperatures. Desert installations may experience temperature swings from below freezing to over 70°C, requiring cables rated for the full temperature range. Coastal installations face the additional challenge of high humidity and salt spray, which can accelerate certain types of degradation.
For moderate UV exposure environments, such as temperate climates with seasonal variations, UV-stabilized PVC or PE cables may provide adequate performance at reasonable cost. These materials typically offer service lives of 10-15 years when properly formulated with appropriate UV stabilizers.
High UV exposure applications, such as desert solar installations or tropical coastal environments, require premium materials such as UV-stabilized TPE or PUR. These materials provide superior UV resistance and can maintain their properties for 20+ years under intense UV exposure, justifying their higher initial cost through extended service life.
Electrical Specifications and Performance Requirements
Electrical requirements form the foundation of cable selection, with voltage rating being the primary consideration. The cable's voltage rating must exceed the maximum system voltage with appropriate safety margins to account for transient overvoltages and long-term insulation aging. Solar installations may require cables rated for 1000V, 1500V, or higher, depending on system design.
Current carrying capacity must be carefully calculated considering installation conditions, ambient temperature, and grouping factors. Cables installed in conduit or cable trays may require derating to account for reduced heat dissipation, while direct burial installations may have different thermal characteristics. The conductor size should be selected to limit voltage drop to acceptable levels while providing adequate current capacity.
Insulation resistance requirements are particularly important for high-voltage applications, as insulation degradation can lead to ground faults and system failures. UV cables must maintain their insulation resistance throughout their service life, even after prolonged UV exposure. This requires careful selection of insulation materials and UV stabilizer systems that do not compromise electrical performance.
Certification and Compliance Requirements
Regulatory compliance is absolutely critical in cable selection, as non-compliant cables may void warranties, insurance coverage, and regulatory approvals. The applicable standards and certification requirements should be clearly identified early in the selection process, as they may significantly limit cable options.
Solar applications typically require compliance with photovoltaic-specific standards such as EN 50618 in Europe or UL 4703 in North America. These standards include specific requirements for UV resistance, temperature performance, and electrical characteristics that are tailored to solar applications.
Building applications may require compliance with construction standards and fire codes that specify particular cable types or fire ratings. Marine applications often require specialized certifications for salt spray resistance and mechanical performance that go beyond standard UV resistance requirements.
International projects may require compliance with multiple standards simultaneously, creating additional complexity in cable selection. It is essential to verify that chosen cables meet all applicable requirements before finalizing procurement decisions.
Mechanical and Installation Considerations
Cable flexibility and bend radius requirements are often overlooked but can be critical for successful installation and long-term reliability. Installations that require tight bending radii or frequent flexing may require TPE or PUR cables that maintain flexibility throughout their service life. Rigid installations may allow the use of less expensive PVC or PE cables.
Connector and termination compatibility should be evaluated early in the selection process, as some cable types may require specialized connectors or termination techniques. The availability and cost of compatible connectors should be factored into the total system cost.
Installation environment considerations include accessibility for maintenance, exposure to mechanical damage, and protection requirements. Cables installed in high-traffic areas may require additional mechanical protection, while cables in remote locations should be selected for maximum reliability to minimize maintenance requirements.
Cost Analysis and Total Cost of Ownership
Initial cable cost represents only one component of total ownership cost, and selecting cables based solely on initial cost often results in higher long-term costs due to premature failure and replacement requirements. Premium UV cables may cost 2-3 times more than standard cables initially but provide 3-5 times longer service life, resulting in lower total cost of ownership.
Installation costs can vary significantly depending on cable type and installation requirements. Flexible cables may reduce installation labor costs by simplifying routing and handling, while rigid cables may require additional support structures or specialized installation techniques. The total installed cost should include cable cost, installation labor, and any additional materials or equipment required.
Maintenance and replacement costs are often the largest component of total ownership cost, particularly for installations in remote or difficult-to-access locations. Cable failures in large installations can result in significant power losses and costly repair operations that far exceed the initial cable cost. Selecting premium cables with longer service lives can significantly reduce these costs.
Supplier Selection and Quality Assurance
Supplier selection is as important as product selection, as cable quality and reliability depend heavily on manufacturing processes and quality control systems. Established manufacturers with proven track records in UV cable production should be preferred, particularly for critical applications where cable failure could have serious consequences.
Quality certifications such as ISO 9001 provide assurance that suppliers have implemented systematic quality management processes. Additional certifications specific to cable manufacturing may be relevant for certain applications or regulatory requirements.
Technical support and application engineering services can provide significant value during cable selection and installation. Suppliers who offer comprehensive technical support, including installation guidance and troubleshooting assistance, may provide better long-term value than those who simply provide products.
Supply chain reliability considerations include supplier financial stability, manufacturing capacity, and geographic distribution capabilities. Large projects may require suppliers with sufficient capacity to meet delivery schedules and provide ongoing support throughout the project lifecycle.
Conclusion
UV cables represent a critical enabling technology for modern outdoor electrical systems, from renewable energy installations to industrial automation and smart city infrastructure. As our world becomes increasingly dependent on reliable outdoor electrical connections, the importance of UV-resistant cables continues to grow. These specialized cables embody decades of materials science research and engineering innovation, providing solutions to the fundamental challenge of maintaining electrical reliability in harsh outdoor environments.
The comprehensive examination of UV cable technology reveals the sophisticated engineering that goes into creating cables capable of withstanding decades of UV exposure while maintaining electrical and mechanical performance. From the careful selection of base polymers to the incorporation of advanced UV stabilizer systems, every aspect of UV cable design reflects the complex interplay between material science, electrical engineering, and environmental durability.
The diverse applications of UV cables, spanning from solar energy systems to marine installations, demonstrate their versatility and critical importance in modern infrastructure. As renewable energy systems continue to expand and outdoor electrical systems become more complex, the demand for reliable UV-resistant cables will only increase. The maritime examples discussed throughout this article highlight the particularly challenging environments where UV cables must operate, from offshore wind farms to coastal industrial facilities.
The technical standards and certification framework surrounding UV cables provides confidence that these products will perform as expected in real-world applications. The rigorous testing protocols established by organizations like ASTM, IEC, and UL ensure that certified cables meet minimum performance requirements while providing manufacturers with clear guidelines for product development. The evolution of these standards reflects the growing understanding of UV degradation mechanisms and the development of more sophisticated testing methods.
The guidance provided for selecting appropriate UV cables emphasizes the importance of matching cable characteristics to specific application requirements. This systematic approach to cable selection, considering environmental conditions, electrical requirements, and total cost of ownership, helps ensure that UV cables provide reliable performance throughout their intended service life. The emphasis on quality suppliers and comprehensive technical support reflects the critical importance of these cables in modern electrical systems.
Looking toward the future, UV cable technology will continue to evolve in response to changing environmental conditions and advancing application requirements. Climate change may drive the development of cables with even greater UV resistance as radiation levels increase in many regions. New renewable energy technologies and smart grid systems may require cables with specialized properties that go beyond current offerings.
The investment in high-quality UV cables represents a fundamental commitment to reliable electrical infrastructure that will serve communities and industries for decades to come. In an era where electrical system reliability is increasingly critical for economic prosperity and public safety, UV cables provide the foundation for dependable outdoor electrical connections. Their quiet, reliable operation enables the technological systems that power our modern world, from the solar panels on our rooftops to the sensors that monitor our cities.
In conclusion, UV cables are not merely electrical components but essential elements of modern infrastructure that enable the transition to renewable energy and smart systems. Their development and deployment demonstrate how focused engineering efforts can overcome environmental challenges and enable the reliable operation of critical electrical systems. As we continue to build more sophisticated and environmentally challenging electrical installations, UV cables will remain essential components that ensure reliable power transmission and system communication in outdoor environments.
How to Reach Us
Get in Touch
SiteMap
Product Catalogue
Reeling Cable
Festoon Cable
Shore Power Cable
Hybrid Cable
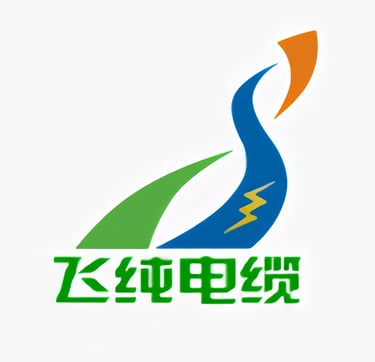
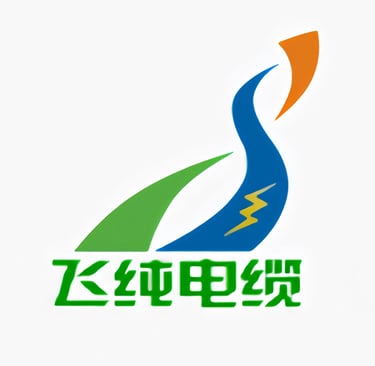
Copyright © 2025 Feichun Australia. All rights reserved.